Scrona, a Swiss inkjet printing pioneer, is making its electrostatic printing technology scalable by utilizing MEMS microfabrication. This allows for the formation of thousands of nozzles on a small area, ensuring high-volume manufacturing capabilities. Unlike conventional inkjet technologies, Scrona’s electrostatic inkjet printing uses electric forces to pull droplets from the outside of the nozzle, resulting in significantly higher efficiency. The technology enables printing with a broader range of materials, including highly viscous inks, and offers printing resolutions as low as 0.5µm. The proprietary MEMS chip, at the heart of the printhead technology, has undergone over a decade of development and will soon be available for industrial applications.
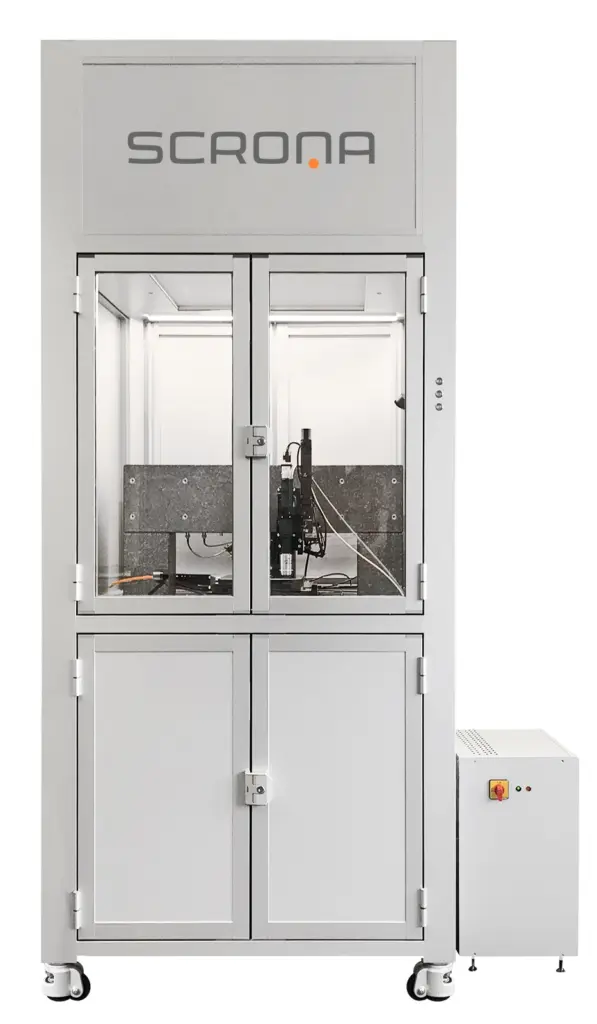
A spin-out of ETH Zurich, the precision achieved by the technology is remarkable, with placement accuracy better than 1um in an array and down to 100nm accuracy. The company’s current second-generation print head features ten nozzles, and the upcoming third-generation system, set to launch in Q1’24, will include 48 nozzles with four different inks. This will eventually scale up to 128 nozzles and larger arrays., which will play a crucial role in enabling new methods for producing MicroLED displays with quantum dots. According to eeNews, the goal of the company is to bring functional printing to areas where additive manufacturing holds immense value. By leveraging MEMS silicon, the technology has already reclaimed the market from laser printers. However, the challenge lied in achieving individual control over the nozzles and reducing the high voltages required for operation.
To address this, the company has developed the first print heads with digital control capability, allowing for precise management of each nozzle. Furthermore, they have successfully implemented electrohydrodynamic (EHD) technology, which operates at voltages below 100V, enabling the use of thousands of nozzles and unlocking production economics.
The scalability of the print heads is crucial for their compatibility with production requirements. Currently, the prototypes feature ten nozzles, but the plan is to develop print heads with 1000 nozzles. Achieving this scale has taken ten years, but the subsequent steps are expected to be faster. The company aims to position the nozzles in custom print heads that align with the pixel array. Each print head, depending on the wafer size, will deposit droplets at a rate exceeding 100kHz. As the company plans for the fourth-generation print head with 1000 nozzles, they are exploring suitable driver technologies. The attachment of MicroLEDs to driver chips remains a challenge, but the company has developed a method of creating electrical connections through bumps on each side of the wafer. They are also working on improving resolution and precision, catering to interests in advanced packaging, back-end processes, and printing materials such as protection and encapsulation.
One significant advantage of the technology is the absence of thermal load during patterning, allowing the use of materials like perovskites. Evaporation is a consideration for high-speed, high-volume production, and the company has developed an active solvent removal system to prevent condensation on the print head. The company has also explored working with various materials, including green-emitting perovskites, indium phosphide, cadmium sulfide, and resins with improved thermal stability.