Researchers at the Georgia Institute of Technology have pioneered a new technique for 3D printing intricate glass structures using a low-temperature process. The method addresses key limitations of current glass 3D printing techniques which require high temperatures and extended processing times.
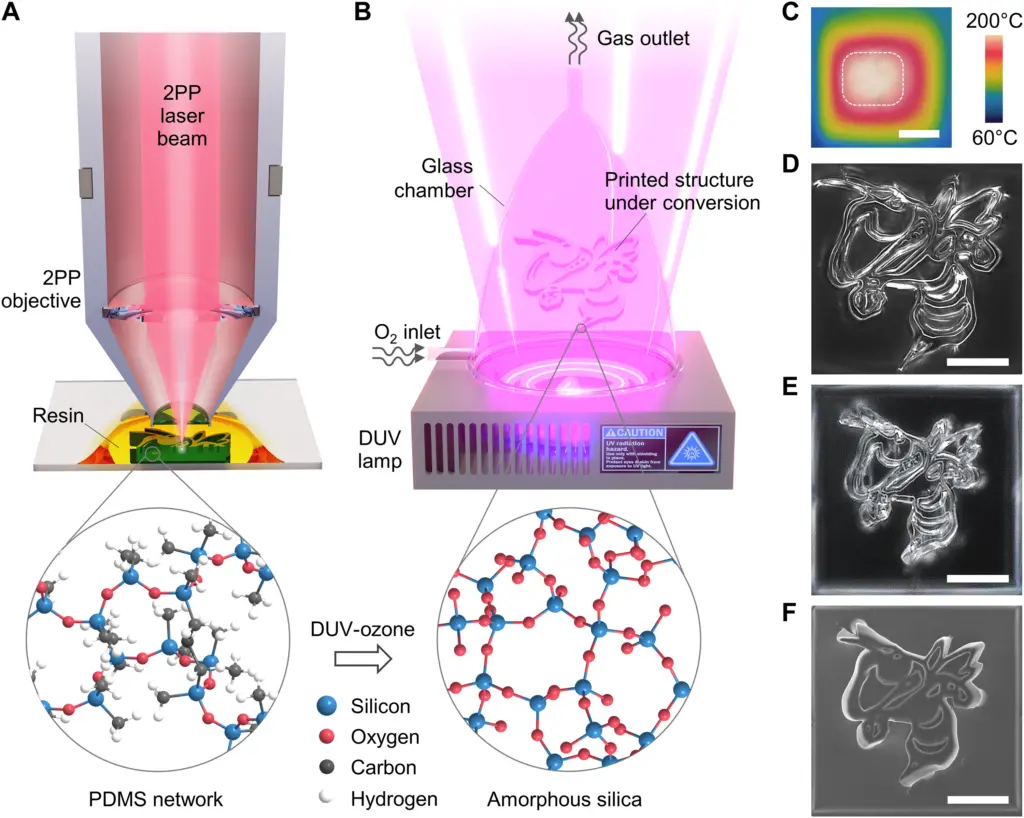
The new approach uses a liquid photosensitive resin made of polydimethylsiloxane (PDMS) as the raw printing material instead of silica nanoparticle-based inks. The PDMS resin is precisely shaped into microscale 3D structures using a technique called two-photon polymerization. The polymer structures are then converted into glass by exposing them to deep ultraviolet (DUV) light in an oxygen environment.
This photochemistry-based process hardens the PDMS into transparent silica glass at just 220°C, far below the over 1100°C needed in conventional glass 3D printing. The conversion also takes less than 5 hours, compared to 12+ hours for existing methods. This makes the new technique more energy-efficient and faster.
The researchers confirmed the PDMS-to-glass transformation using chemical analysis. They successfully printed complex 3D microstructures like miniature lenses and microfluidic channels with excellent precision and optical clarity.
The new low-temperature glass printing technique enables the cost-effective fabrication of intricate glass microcomponents for applications in optics, electronics, medical devices, and microfluidics. The researchers are now focused on scaling up the process to print larger millimeter-scale glass structures.
Reference
Mingzhe Li et al., Low-temperature 3D printing of transparent silica glass microstructures.Sci. Adv.9,eadi2958(2023).DOI:10.1126/sciadv.adi2958