Display Week has always been a place to get a glimpse of the future of display technologies with outstanding symposium paper presentations, seminars, short courses, business conference, panel discussions and exhibitions of new products. This year’s conference was able to give great insights about current status of MicroLED displays, critical challenges and requirements for future success. MicroLED display technology is starting to mature, but will there be enough momentum to resolve the challenges: high-volume manufacturing, supply chain integration, production cost reductions to create new opportunities for the application markets?
Diminished Market Outlook Forecast
According to Ross Young CEO of DSCC, in his keynote presentation at the Business Conference, “Apple’s exit after 10 years and more than $1B spent has resulted in many companies rethinking their involvement in MicroLEDs with a number of companies exiting the category and others delaying their programs.” With Apple’s exit, DSCC’s MicroLED wearable market outlook is considerably smaller, their 2027 forecast is about $1B less.
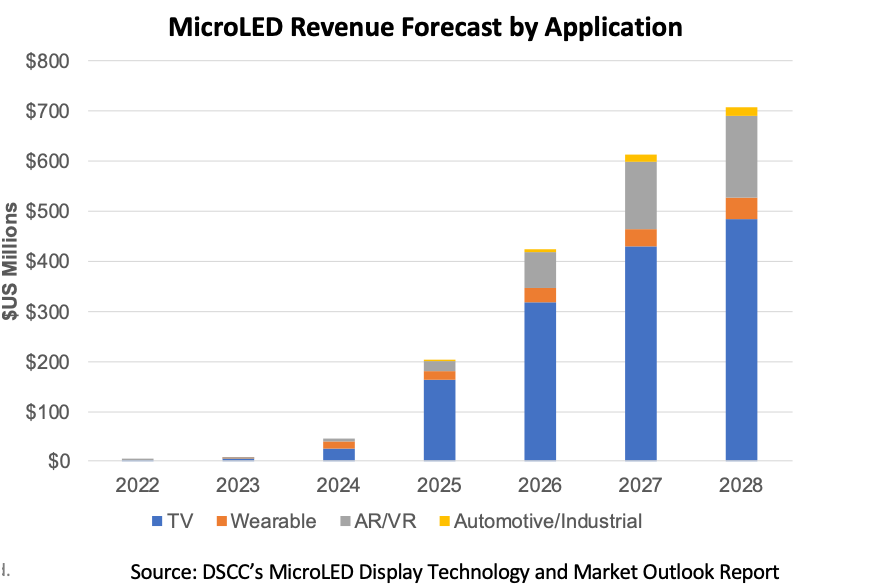
Eric Virey, Senior Display Analyst from Yole Intelligence said in his symposium presentation, “On February 28th Apple canceled the MicroLED project, undermining the trust in the technology and prospect”. He said that the industry has already spent $11.9 B on MicroLED development by end of 2023. From that total spending, $7B was from companies outside of Apple’s MicroLED ecosystem. There has been a lot of delays and scale-back in projects after the Apple decision. As he pointed out – This is a problem as OLED keeps improving and MicroLED being delayed and value proposition for MicroLED is declining. That is creating urgency in the industry to accelerate commercialization.
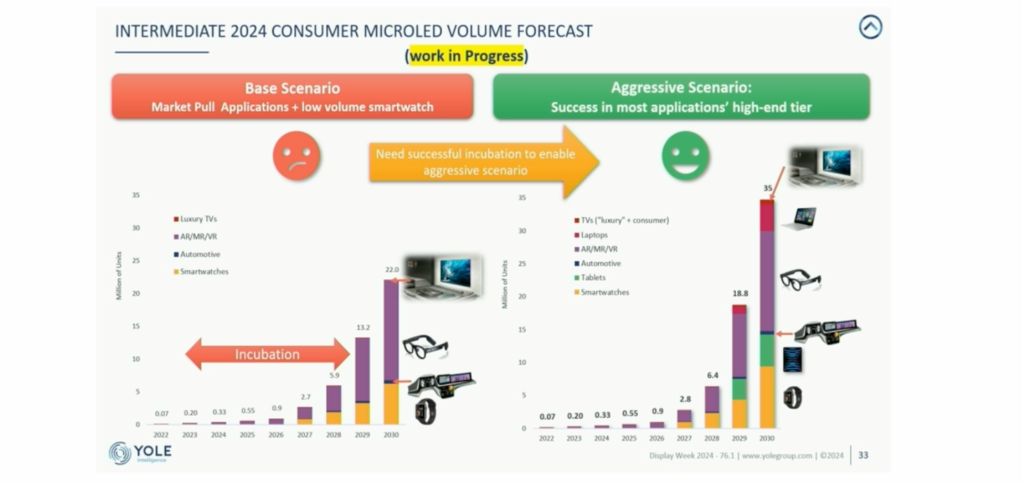
Innovative Mass Transfer Process
In a very insightful panel discussion, moderator Bob O’Brien (cofounder and CFO of DSCC) asked industry executives from Samsung, BOE, Applied Materials and AUO, “MicroLED looks beautiful and has great performance but what are the challenges for high volume manufacturing?” Applied Materials’ VP Nag Patibandela said, “Manufacturing supply chain maturity is the key enabler to get us to next stage.”
AUO’s CTO Dr. Wei Lung Liau said, “It is high costs. First there is need to reduce MicroLED chip size and enlarge MicroLED mass transfer process generation and throughput”. Dr. Jong-Moo Huh corporate VP for Samsung Display said, “Performance, production cost, productivity are critical. For mass production we still need innovative process for transfer and bonding.” According to Alex Chen CTO of BOE, “We still need to find most efficient way for the mass transfer”.
As per equipment company Toray’s presentation in the Business Conference, by Account Manager Katsumi Araki, “To achieve true high-volume production, challenges are high throughput transfer for productivity, efficient 1st and 2nd repair process and large size substrate bonding such as Gen 4.5 and Gen 6. There is need for inspection process collaboration, laser direct transfer, laser trimming, cutting and bump transfer for 1st and 2nd repair and new large size bonding machines”. He said new collaboration to achieve more trustable process is needed. (e.g. collaboration with VueReal MicroSolid Printing platform).
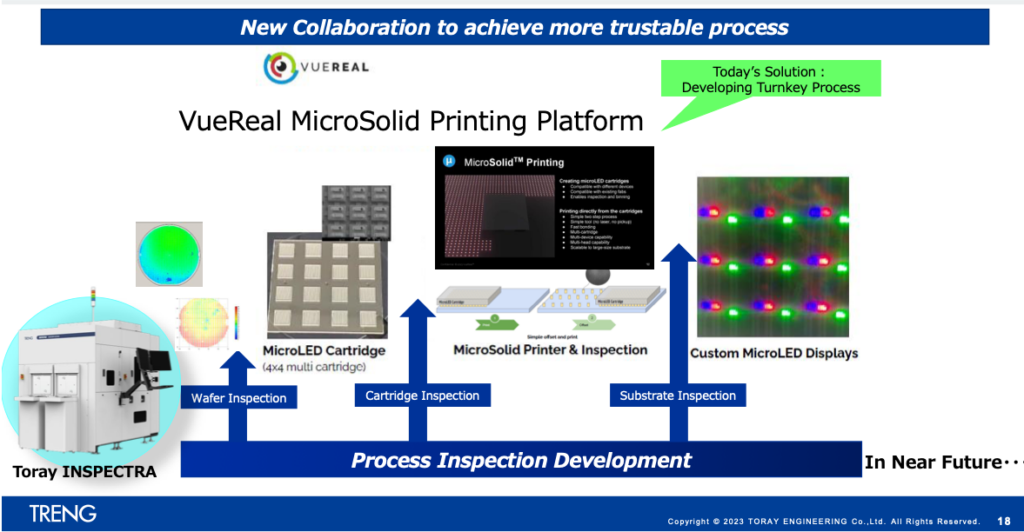
Vue Real CEO and founder Reza Chaji said in my meeting with him at DisplayWeek, “Transfer is the big issue as it has direct effect on material cost plus yield”. He said in his business conference presentation, “Device and backplane innovations hit a unit cost/performance wall without advances in Transfer. To enable market opportunities core technology is transfer platform”.
According to the company information their MicroSolid printing transfer technology enables >99.999% yield, throughput 2 times faster than pick and place or laser, managing wafer non uniformity with cost competitiveness (even for smartphone) and scalability (4 times more display/wafer capacity). At Display Week 2024, VueReal introduced Quantum Vue display technology that integrates MicroSolid Printing platform with Dynamic QD patterning to enhance display reliability, performance and brightness, while reducing production costs for larger displays.
BOE CTO Alex Chen also said in the panel discussion, “The TFT MicroLED is based on Gen 5.5 or Gen 6, but most mass transfer is based on semiconductor sizes such as Gen 2.5. There is a mismatch for cost and production efficiency. If industry focuses on small sizes for backend it cannot compete with OLED cost.” Yield of LED itself also is an issue. There is a need for efficient ways to test LED and do repair work after mass transfer.
InZiv presentation at the Business Conference reported, “Poor inspection solutions lead to low yields and high costs. Smaller MicroLEDs exacerbate the problem. There is a critical need for effective inspection equipment. EL (Electroluminescence) is most critical measurement in MicroLED inspection”. It provides electrical information and closely replicates the method of chip emission in device. At the same time EL measurement requires contact that can lead to severe damage of small devices. Standard probing of EL is very slow. As InZiv presentation showed EL is the critical bottleneck in MicroLED mass manufacturing today. InZiv is developing substrate level (Gen 3.5-4.5, Gen 6, Gen 8) in accordance with customer requests in 2025+ timeframe. This can help MicroLED development.
Integrated Supply Chain and Standardized Process
For cost reductions MicroLED needs more integrated and matured supply chain. As AUO’s CTO Dr. Liau said in panel discussions, “Improvement of cost needs close cooperation of chip, equipment and display companies.” AUO has strengthened the MicroLED ecosystem by investing in Enostar and Playnitride. That has enabled AUO to have 1st one campus mass production line with technology transfer from Playnitride integrated in mass transfer and TFT backplane line. It has increased efficiency, yield and reduced cost. AUO started first mass production at the end of 2023 and decided to invest in higher generation line in 2025. AUO showcased world’s largest single piece MicroLED display 31-inch at DW 2024. BOE has invested in HC SemiTek LED manufacturer in China. BOE CTO expressed the need for deep cooperation of leading consumer brands, equipment companies, LED companies and display companies. Higher confidence on each other will accelerate development.
So far MicroLED supply chain is fragmented compared to LCD and OLED as technology is not standardized yet. Materials and processes are very diversified, with options for flip chips or vertical chips and mass transfer can be pick and place, laser, stamp or some new solutions. Most of the panelist for MicroLED believe that ,when supply chain gets matured like LCD and OLED more value chain partners will join together and cost will go down. Without inhouse development any change in chip structure or process takes very long development time. Also, it makes it difficult to target a BOM cost to meet application requirements. MicroLED cost outlook is still way higher than OLED making it difficult to compete. For cost improvements, density increases with reduction in die size and efficiency improves at the same time. Size reduction also leads to issues with transfer, bonding, yield as well as testing. Panelist felt 10 microns may be okay for direct view applications and 2 microns will be good for micro display applications.
Product Differentiation for Market Expansion
Jennifer Lin, VP of AUO presented that MicroLED can have infinite possibilities with features such as high transparency, perfect HDR, sunlight readability, free viewing angle, seamless tiling, free form factors and sensor integrations but challenges are cost (chip price, throughput and product yield), power efficiency and mura free tiling calibration. MicroLED.
AUO is focusing on applications such as watch, automotive (interactive transparent window, rollable rear seat entertainment), indoor cinema and transparent display (some developing transparent notebooks and monitors). Sensor integration is one of the unique capabilities of MicroLED that differentiates it from other displays. AUO also showed MicroLED with under-display camera. It has developed a MicroLED on top of LCD creating 3D display suitable for car cluster or casino application.
Max McDaniel, VP and CMO of Applied Materials display group’s presentation said, “MicroLED allows more real estate for convergence of devices on panel”. That will lead to growth of embedded sensors and devices in displays leading to future smart products where display will integrate muti function such as voice recognition, eye tracking, biometrics, virtual tactiles and toxic gas detection.
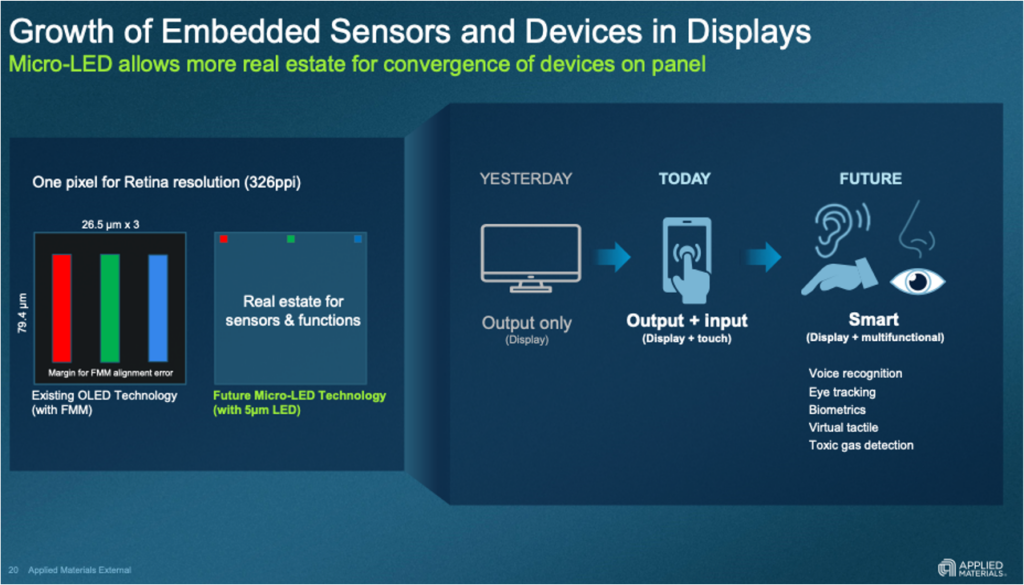
Broad ranges of prototypes were shown at Display Week 2024 exhibitions. Some protypes of MicroLED display at the conference are listed below:
- AUO: Best MicroLED-based Technology award for 60” transparent (60% transparency) Tiled display, 600 nits, 31’ single panel MicroLED LTPS backplane, 500 nits, 17.3” 1000 nits foldable MicroLED , 13.5” transparent (50% transparency) auto display 5000 nits, 13.5” display integrated with under camera & sensor, 30” transparent MicroLED display placed on LCD display creating 3D
- Innolux: 1.63” 403 PPI (LTPS backplane) display for wearable, 8.7” auto transparent (55% transparency) 1500 nits, 106” AM MicroLED free Tiling display (96x 12.3”) QD color conversion
- Tianma: 8.07” Octagon- shape transparent (55% transparency), 1500 nits, 176 PPI MicroLED display for automotive (digital side mirror), 1.63 403PPI, wearable display, 7.6” 5000 nit panel
- TCL/CSOT: 163” 4K Tiled MicroLED display, 10,000 nits
- Playnitride: PCB based six sides cube MicroLED display RGB flip chip, for signage application, 9.3” transparent display bonded with LCD to change transitivity from 1% to 40%
MicroLED display industry has momentum even after Apple’s exit. Supply chain is still not mature, integrated or standardized like LCD or OLED. With mass transfer testing issues and high costs, high-volume mass production is not ready at this time. Display suppliers such as AUO are already starting mass production. Suppliers of LED, display and equipment are also working towards better integrations, higher generation equipment and more innovative solutions for manufacturing efficiency to reduce costs.
MicroLED displays can expand the application market with new features such high transparency, sensor integrations, tiling, free size and form factor.
In future, can there be a paradigm shift for display – from flat to flexible to freeform?
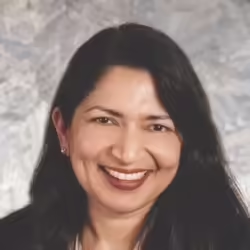
With more than 26 years of experience in the Display Industry and Display Market plus technology research, Sweta is a highly sought-after consultant and a frequent advisor to firms that invest in the Display value chain. Prior to starting Dash-Insights, Sweta was the Senior Director of Display Research, and Strategy at IHS Technology, and was the head of applied research, consulting, strategy, and Display Expert.