Applied Materials has introduced a new method for creating full-color MicroLED displays using innovative quantum dot (QD) technology. MicroLED displays have been gaining attention due to their impressive luminance and energy efficiency. These displays are particularly suitable for near-eye applications, direct-view displays, automotive uses, and large-format installations like TVs and video walls. However, the high manufacturing costs and yield challenges have hindered their widespread adoption.
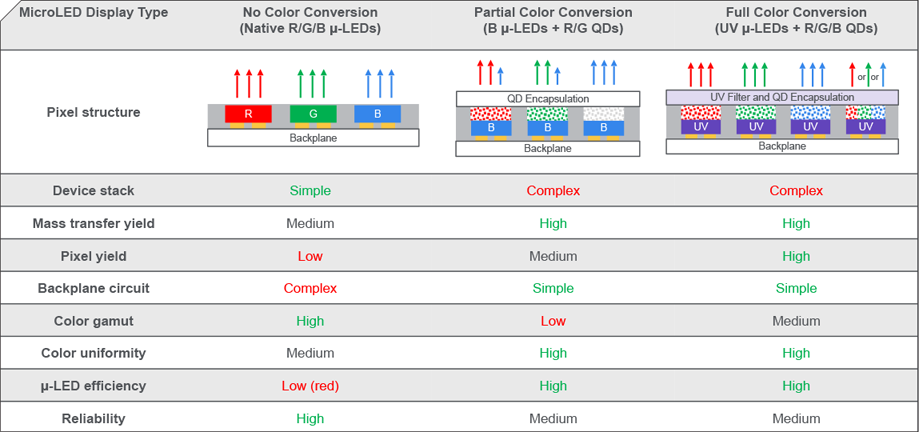
The research, led by Mingwei Zhu and his team at Applied Materials, compares various architectures and manufacturing methods for MicroLED displays, highlighting the full-color conversion approach. This method uses UV MicroLEDs with red, green, and blue (RGB) QDs, offering several advantages over traditional approaches.
Three primary methods for assembling RGB full-color MicroLED displays are discussed: native RGB MicroLEDs, hybrid structures (partial color conversion), and full-color conversion. The native RGB approach, despite its straightforward assembly, struggles with low luminescence efficiency and complex backplane circuit design. The partial color conversion method simplifies manufacturing but compromises color purity. In contrast, the full-color conversion approach using UV MicroLEDs and RGB QDs streamlines manufacturing, enhances color uniformity, and improves pixel yield.
Quantum dots, semiconductor nanocrystals with exceptional light-emission properties, play a crucial role in this new approach. The research categorizes QDs into Cd-containing, perovskite-based, and indium phosphide (InP)-based. While Cd-based QDs offer excellent color purity and efficiency, environmental concerns due to their toxicity drive the industry towards Cd-free alternatives. Perovskite QDs provide high efficiency but lack stability. InP-based QDs, though with a broader emission spectrum, are gaining traction for their acceptable performance and safety.
Applied Materials is leading the development of Cd- and Pb-free QDs using a 385-nm UV MicroLED excitation source. These QDs, comprising InP-based red and green QDs and ZnSe-based blue QDs, offer significant UV light absorbance and environmental benefits. The integration process ensures QD stability, demonstrating their potential for high-performance displays.
The QD pixel fabrication process uses photolithography and inkjet printing as key methods. Photolithography, suitable for high PPI displays, involves creating a QD photoresist, while inkjet printing, preferred for large-area displays, ensures precise QD placement. The innovative printing-curing-washing-drying (PCWD) process developed by the team employs industrial-scale piezo-based inkjet printing, followed by selective UV curing, to achieve precise QD placement and prevent color bleed.
A 1.37-inch smartwatch display prototype using UV MicroLEDs and RGB QDs is showcased in the research, achieving a pixel density of 318 PPI, luminance over 3,000 nits, and a high contrast ratio. The display covers over 90% of the DCI-P3 color gamut, with potential improvements to 99% through enhanced pixel isolation. The angular light-emission pattern of QD color-conversion MicroLEDs shows superior uniformity compared to GaN-based MicroLEDs, OLED, and LCD displays.
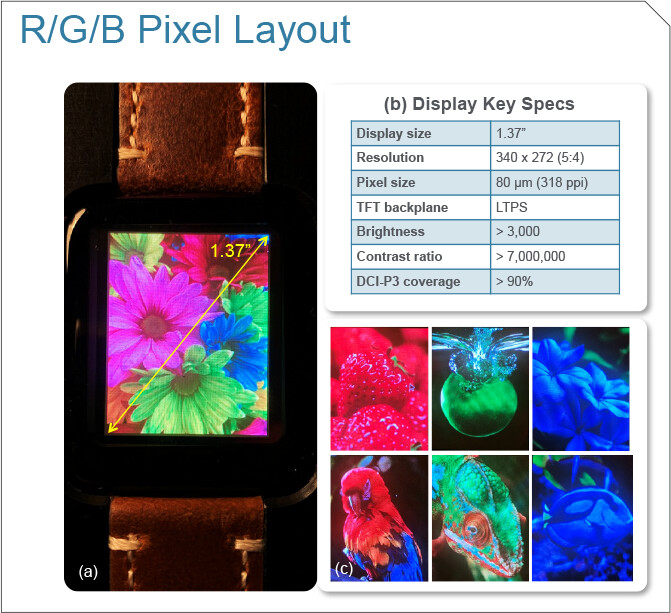
Despite the promising advancements, challenges remain. Improving LED efficiency at low current densities, addressing carrier loss at MicroLED sidewalls, and ensuring QD stability are critical areas for further development. Encapsulation techniques and enhanced QD synthesis are essential for mitigating degradation and achieving long-term stability.
Reference
Zhu, M., Ganapathiappan, S., Sivanandan, K., Ding, K., Ng, H. T., Li, Z., & Patibandla, N. (2024). MicroLED Displays from Full-Color Conversion: A Practical, Manufacturable Approach. Information Display, 40(3), 20–25. https://doi.org/10.1002/msid.1485