Miniaturized light-emitting diode (MiniLED) backlight technology represents a significant advancement in the evolution of display technology. This development builds upon the strengths of traditional light-emitting diodes (LEDs) and seeks to bridge the performance gap between liquid crystal displays (LCDs) and organic light-emitting diode (OLED) displays.
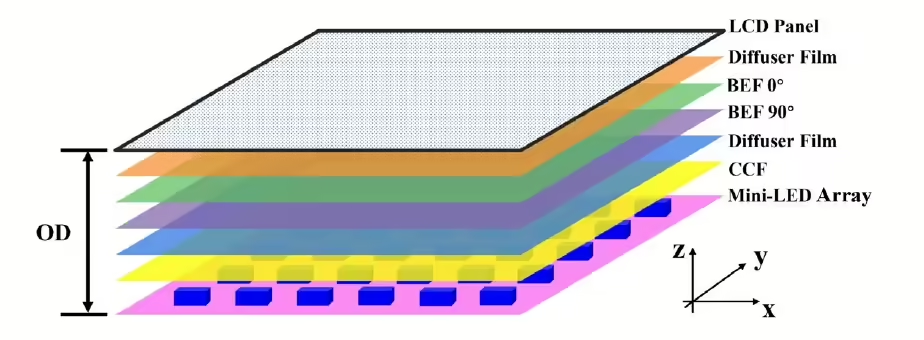
MiniLED technology has become highly relevant due to its potential to enhance the brightness, contrast ratio, and power efficiency of LCDs, offering display qualities that approach or even rival OLEDs. With their compact size, typically ranging from 100 to 200 micrometers, MiniLEDs enable local dimming on a much finer scale than conventional LEDs. This local dimming capability allows for HDR (high dynamic range) effects by dividing the backlight into multiple dimming zones, each of which can be individually controlled. By maintaining some of the advantages of LED technology while addressing many of its limitations, MiniLED backlights have carved out a prominent role in the consumer electronics industry, particularly in television and monitor displays. Despite this progress, technical challenges such as the halo effect, color consistency, and efficient driving schemes remain areas of active research.
At the heart of MiniLED backlight technology lies a range of packaging innovations that enhance the performance and manufacturability of MiniLED displays. The primary packaging techniques are Package on Board (POB), Chip on Board (COB), and Chip on Glass (COG), each with its strengths and limitations. POB, the most mature and widely adopted technology, uses traditional surface-mounted device (SMD) technology, making it cost-effective. However, its relative thickness limits the potential for ultra-slim designs. In contrast, COB integrates the LED chips directly onto a circuit board, producing brighter and more uniform backlight displays due to the closer chip arrangement. Although this approach is promising, COB’s manufacturing process requires higher precision and suffers from lower yields, making it less cost-effective for mass production. COG, which is even more advanced, replaces the circuit board with a glass substrate. This technique allows for even thinner designs, enabling large-format applications while maintaining high brightness and resolution. However, COG is still emerging and faces significant technical and economic challenges. While each packaging technology offers unique benefits, advancements in manufacturing processes and cost reduction strategies are crucial to making MiniLEDs accessible for broader market adoption.
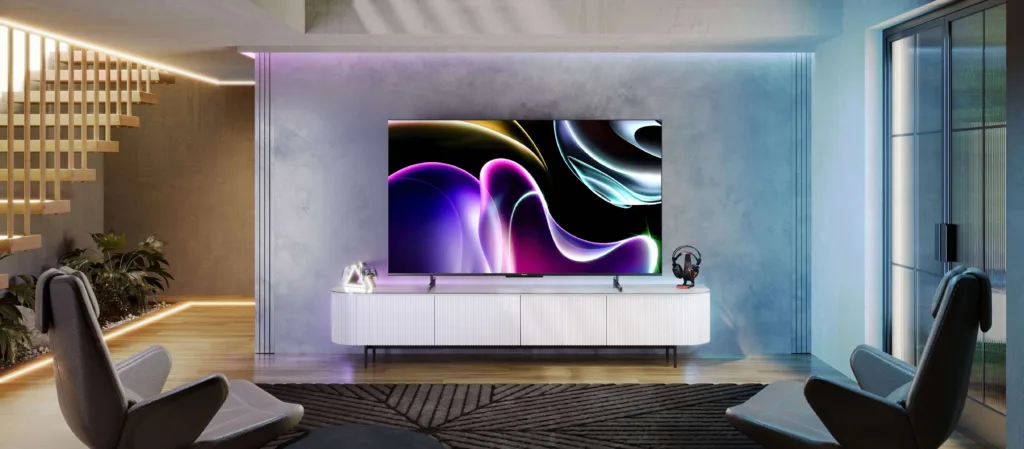
MiniLED backlight displays also rely on sophisticated color conversion methods to produce vibrant and accurate colors. Traditional RGB LEDs are often supplemented or replaced by techniques involving phosphors and quantum dots (QDs) to create a broader color spectrum. Phosphors, commonly used in MiniLEDs, involve embedding rare-earth-doped green phosphors and narrow-spectrum red phosphors around blue LED chips to produce white light. This approach ensures that the backlight’s spectrum closely matches the transmittance bands of RGB color filters in LCD panels, resulting in high color accuracy. Quantum dots provide another innovative solution; by adjusting their size, QDs can emit different colors of light, producing a backlight with a wider color gamut. Compared to conventional displays, MiniLED displays using QD technology have achieved an NTSC color space coverage of over 110%, enhancing the color depth and realism of the image. However, QDs present challenges regarding temperature stability and environmental impact, particularly for materials containing toxic heavy metals. To address these issues, researchers are developing QDs that use non-toxic materials and are more resistant to temperature fluctuations and environmental degradation. The improvements in color conversion techniques are critical to the overall appeal of MiniLED displays, as they significantly impact color vibrancy and viewing quality.
The ability to achieve high contrast ratios and HDR effects is central to MiniLED backlight technology, primarily accomplished through local dimming. Traditional LCD backlights provide uniform brightness across the screen, resulting in a washed-out look in dark areas and increased power consumption, as all backlights remain fully lit even when only part of the image requires brightness. MiniLED backlights address this issue by dynamically adjusting brightness based on the image content. Local dimming divides the screen into zones, each with independent brightness control, to enhance contrast ratios by allowing darker regions of the screen to remain dim while other areas are fully illuminated. There are two primary local dimming configurations: one-dimensional (1D) dimming, which organizes LEDs in a single row or column, and two-dimensional (2D) dimming, which allows finer control by creating a grid of dimming zones across the entire backlight. Two-dimensional dimming is especially effective in high-contrast scenes, significantly improving the visual quality by creating deep blacks and bright whites without excessive power consumption. Despite these advancements, local dimming faces technical hurdles, such as increased power consumption due to additional LEDs and the complexity of driving schemes.
Driving schemes play a critical role in managing the MiniLED backlight’s dimming zones. The two main driving methods for MiniLED backlights are passive matrix (PM) and active matrix (AM) driving. PM driving, the more established approach, is advantageous in scenarios where fewer dimming zones are required. It involves either static driving, where each LED is controlled individually, or dynamic scanning, which lights LEDs sequentially in rows or columns, thus reducing power consumption. Although PM driving is compatible with current production methods, it struggles to handle the larger number of dimming zones necessary for high-resolution displays. Active matrix driving addresses these limitations by allowing independent control over each LED in a dimming zone, providing greater precision and minimizing visual artifacts in high-resolution images. However, AM driving’s high complexity and cost hinder its widespread adoption. Integrating AM driving with affordable materials, such as glass substrates, could potentially overcome these barriers, yet significant technical challenges remain.
The halo effect is another issue that impacts the visual quality of MiniLED displays. The halo effect occurs when light from bright regions of the screen spills into adjacent dark areas, reducing image contrast and clarity. This problem is especially pronounced in displays with high-resolution panels and numerous dimming zones, as smaller pixel sizes make these optical artifacts more noticeable. To mitigate this effect, engineers are experimenting with optical structures, such as lens collimation and bank isolation, that restrict light leakage between dimming zones. Adjustments in backlight design, such as decreasing the LED’s optical aperture and reducing the optical distance between the backlight and the LCD panel, can also reduce halo effects but may compromise backlight uniformity and complicate thermal management. Algorithmic solutions have also shown promise, with advanced local dimming algorithms that analyze the image’s brightness distribution to modulate the backlight intensity and reduce visual artifacts. For example, convolutional neural network (CNN)-based algorithms can dynamically adjust dimming values based on scene content, minimizing the halo effect in real-time applications. Although these strategies improve halo suppression, the complexity and cost associated with these methods underscore the need for further refinement to achieve optimal visual quality at a reasonable price.
Looking forward, MiniLED technology continues to hold tremendous promise for enhancing LCD performance and bringing it closer to OLED-like quality. However, several key challenges must be addressed before MiniLED displays can reach their full potential. As the number of MiniLEDs in a display increases, managing heat dissipation becomes critical. Emerging packaging technologies such as COB and COG, although not yet commercially viable on a large scale, offer solutions by improving heat dissipation capabilities. Integrating quantum dot materials into backlight systems can enhance energy efficiency and expand the color gamut.
Dimming algorithms remain another area of improvement, as current algorithms may not perform consistently across different image types. Developing adaptive algorithms that can handle a wide range of content types and integrate seamlessly into hardware is essential. Despite ongoing advancements, the halo effect continues to challenge MiniLED technology. Because the halo effect arises from optical crosstalk between adjacent dimming zones, improving local light confinement remains an effective approach to reducing this phenomenon.
References
- Chen, J.-H., Huang, C.-H., Lee, T.-Y., Chen, F.-C., Kao, T.-S., & Kuo, H.-C. (2024). Advancing LED technology: The FDCSP element’s breakthrough in mini and micro-LED packaging and backlight module enhancement. Discover Nano, 19(1), 94. https://doi.org/10.1186/s11671-024-04033-5
- Lei, J., Zhu, H., Huang, X., Lin, J., Zheng, Y., Lu, Y., Chen, Z., & Guo, W. (2024). Mini-LED Backlight: Advances and Future Perspectives. Crystals, 14(11), Article 11. https://doi.org/10.3390/cryst14110922