Adding haptic technology with a tactile touch sensation to touchscreen displays has become a significant design trend within many industries.
Automotive, industrial and medical interfaces where the users can’t always visually confirm touchscreen actions are clear areas of need for haptic technology. While a number of solutions exist, all involve tradeoffs in terms of size, power and functionality
The new TDK piezo actuator/sensor, called PowerHap™, uses voltage to create displacement when providing haptic sensations. But it can also be used in reverse to use mechanical motion to create voltage, which can be used to trigger the haptic feedback (sensor mode).
The series is offered in three sizes: 15G, 7G and 2.5G (referring to the acceleration it can deliver on a mass of 100 g). It uses an innovative multi-layer design that creates the highest acceleration and force on the market today and allows for (relatively) low voltage operation. The slim square plate consists of 23 layers with displacement amplifiers on both sides. Applying voltage creates a small expansion of the piezo ceramic in the z (out-of-plane) direction – around 1.5 microns. But the voltage also creates an even larger contraction of the plate in the x and y directions that varies from 4 to 6 to 13 microns depending on the actuator size.
Note that these actuators can require up to 120 volts – not exactly typical CMOS levels. To date, this has been a big problem with existing drivers which consume a fair amount of power. To solve this problem, Boréas Technologies has developed a new driver architecture that departs from the audio-centric designs of the past to offer a step change in performance and power consumption. Boréas Technologies CEO Simon Chaput noted that, “Our new driver offers 6X faster response time (<1ms) and 10X lower power consumption compared to existing solutions. This makes it ideal for any mobile application.”
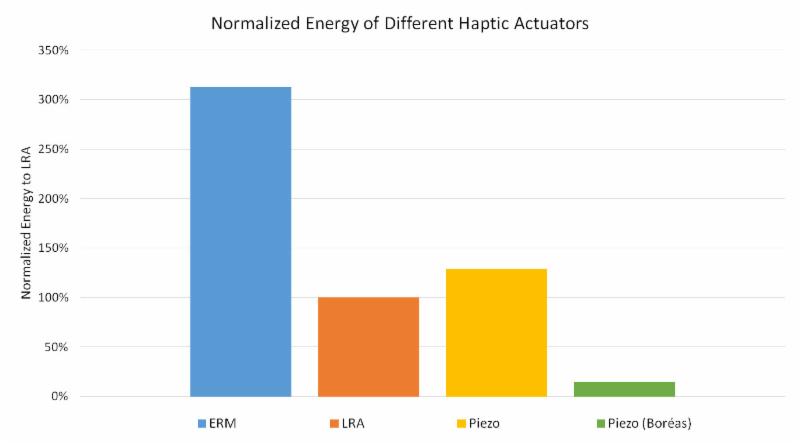
Chaput also provided a comparison chart showing an energy use comparison with the existing piezo drivers and two other popular haptic solutions: Eccentric Rotary Mass (ERM) devices and Linear Resonant Actuators (LRA) which are already used in devices like your smartphone. And, the new driver is tiny – just 4 x 4mm in a standard QFN package.
What is great about the PowerHap series is the ability of the actuator to cover the full range of human touch sensitivity. That’s because the piezo actuators can be driven with a variety of signals with different shapes and frequencies. The shape and frequency of the signal can impart a different “feel” while the amplitude can set the intensity or impact that the signal has on the person. High amplitude signals can deliver strong displacement and G forces providing very positive feedback signals – like a button click.
According to Professor Hong Z. Tan, a haptics expert at Purdue University, “The human touch threshold is dependent upon the frequency of the signal and we are more sensitive to signals above a frequency threshold that is around 100Hz. What that means is that at 300 Hz, a displacement of only 0.1 micron can be detected but if the stimulus is at 3Hz, one needs a displacement of 10 microns to feel it. Generally, you want to deliver signals that are about 10-20 dB above the threshold to be readily detectable.”
Professor Tan then described how signals at different frequencies can feel. “A 10-15 Hz signal feels like ‘flutter,’ a 30-50 Hz signal feels ‘rough’ (like a jack hammer), and above 100 Hz , the sensation is ‘smooth vibration’,” continued Tan.
The chart below shows the performance envelopes of the three PowerHap actuators. Note that all are well above the human detection threshold over a wide range of frequencies vs. the LRA solution with a narrow frequency range.
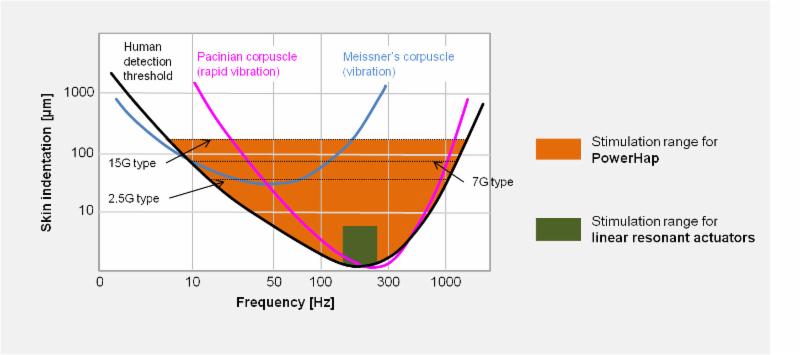
Another important feature of the PowerHap actuator and Boréas driver combination is the ability to deliver a very low latency response speed of less than 1ms at the system level – not just the actuator. Low latency is important to get fast feedback so the user doesn’t keep pressing a button or pressing harder because the haptic response to the touch was too slow.
Finally, TDK summarized the PowerHap performance specifications compared to competitive technologies.
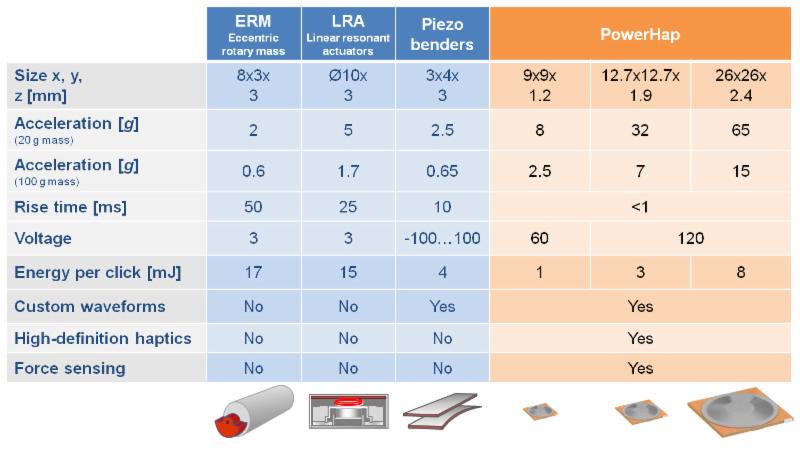