Researchers at Seoul National University of Science and Technology (SEOULTECH), led by Professor Sumin Kang, have developed an innovative technique to address long-standing challenges in the manufacturing of ultrathin displays for electronic devices. The demand for thinner, lighter, and more flexible displays has grown rapidly in recent years, and ultrathin polyimide (PI) films are widely used as substrates due to their exceptional thermal stability and flexibility. However, traditional laser lift-off (LLO) techniques, used to separate PI films from their carrier substrates, often fail when applied to films thinner than 5 μm. These techniques typically result in mechanical deformation, wrinkling, and residue, compromising the quality of ultrathin displays.

The limitations of conventional LLO methods arise from the strong adhesion between the PI film and its carrier substrate, which leads to high mechanical strain during laser ablation. To overcome these challenges, the research team at SEOULTECH has introduced the Graphene-Enabled Enhanced Laser Lift-Off (GLLO) method. This approach incorporates a layer of chemical vapor deposition (CVD)-grown graphene between the PI film and the glass carrier, creating a new approach to the separation process.
Graphene’s ability to absorb ultraviolet (UV) light shifts the ablation site from within the PI film to the graphene-PI interface, reducing the amount of carbonaceous residue left on the carrier. Additionally, graphene’s high in-plane thermal conductivity facilitates lateral heat diffusion, which smooths the blister formed during laser ablation and reduces mechanical strain on the PI film. Graphene acts as a barrier to reduce interfacial adhesion, allowing for smoother separation and minimizing damage to the ultrathin films.
This novel method has proven to be a significant improvement over conventional LLO techniques, according to the researchers. The GLLO process successfully separates PI films as thin as 2.9 μm without causing significant damage, addressing a critical need in ultrathin display manufacturing. Moreover, the process is more robust and reliable, offering a wider range of laser fluences and scanning pitches for successful operation. The graphene layer minimizes wrinkling, rupturing, and residue on the PI film, enhancing the overall quality of the separated films. The reduced residue left on the glass carrier creates potential for its reuse, offering cost-saving opportunities in the manufacturing process.
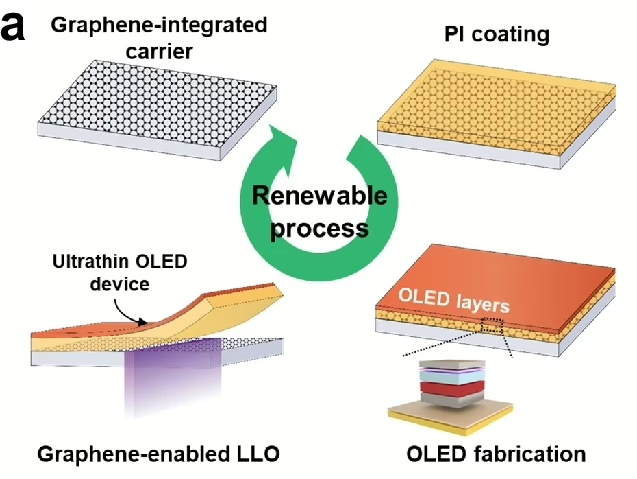
Extensive experimental validation has demonstrated the efficacy of the GLLO method. The researchers compared the process windows of GLLO and traditional LLO, finding that GLLO offers a significantly broader process window and reduced surface roughness. Residue analysis revealed that the graphene layer dramatically minimizes the thickness of carbonaceous residue on the carrier, and confocal microscopy confirmed the smoothing effect of graphene on blister formation during ablation. The researchers successfully used the GLLO method to separate ultrathin organic light-emitting diode (OLED) devices fabricated on 2.9 μm PI substrates. These devices retained their electrical and mechanical performance even under extreme deformation, demonstrating the method’s suitability for flexible and wearable electronics.
Initial results also highlighted the potential for reusing graphene-integrated glass carriers across multiple OLED fabrication cycles, further enhancing the sustainability and cost-effectiveness of the process. However, additional optimization is required to achieve complete residue elimination, and ongoing research will focus on refining this aspect of the technique.
Reference
Kang, S., Chang, J., Lim, J. et al. Graphene-enabled laser lift-off for ultrathin displays. Nat Commun 15, 8288 (2024). https://doi.org/10.1038/s41467-024-52661-3